Today I’m talking to Oliver Goodyear, Engineering Manager at Michael Aubrey Partnership about the main issues associated with fire escape inspections and how we helped a recent client.
What Are The Main Issues That You Encounter When Carrying Out A Fire Escape Inspection?
One of the main issues with these types of structures is that they are rarely used and, in most instances, never tested for a mass egress scenario, as fortunately fires are rare.
But because of this, these structures are often found neglected and left to deteriorate.
Unfortunately, we are finding that there are an alarming number of inadequate staircase structures out there, that may struggle to provide their intended function at their hour of need.
What Do You Normally Look For During A Fire Escape Inspection?
In general, we are looking at two items. Firstly, is the fire escape staircase structurally safe, i.e would it support the load imposed by a mass egress scenario?
We do this by checking the structural condition of each staircase component and connection.
Most staircases are usually steel and we find deterioration due to corrosion is the most common defect.
However often we are finding the corrosion is exacerbated by poor detailing (leaving somewhere for water to collect), the wrong type of bolt or even the wrong type/poorly applied paint.
Secondly, if the staircase is deemed structurally safe, the other item we assess is whether the staircase itself is safe to use in terms of functionality.
We often try to align this with Building Regulations and check that the
- surface is grippy
- the handrails do not have large gaps which may present a fall hazard to children
- there are no obstructions to the escape route.
We have had instances in the past where say a satellite dish over sails the staircase and would cause a head clash or where bird waste or litter is left to congregate on the stairs.
Often menial and easy to resolve items, that would make a massive difference if the staircase is called into use.
What Happened At This Particular Site?
This particular site was a school in Brighton.
So automatically we were thinking high salinity in the air (steel structures tend to have shorter lives in these environments, often regularly meaning maintenance and recoating).
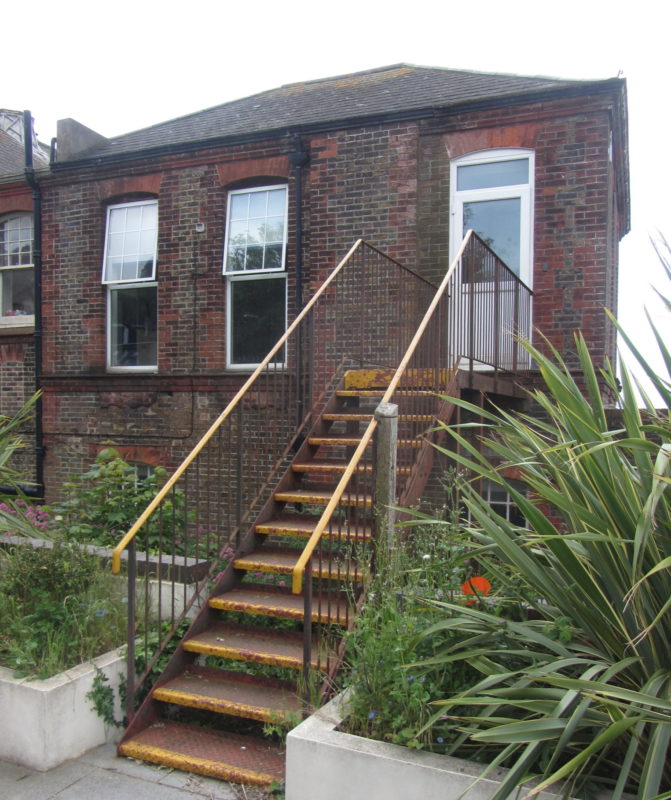
This particular staircase was a straightforward single flight and landing serving a first-floor landing and was noticeably rusty.
Painted System – Regular Maintenance
The superior corrosion protection for these types of structure is usually a galvanised structure.
This one was a painted system, which was fine but usually needs more regular maintenance and in this instance the paintwork was worn, and the steel was corroding.
The corrosion was fairly advance, and sections of the steel structure were beginning to delaminate/break apart.
Worst Affected Area
The worst affected area was to the base of the column, where two of the columns had failed and the square tube had been completely eaten through with corrosion.
This is a common issue with steel tubes in contact with the ground as water can become trapped inside the tube and eaten away at both the inner and outer faces, which had occurred in this instance.
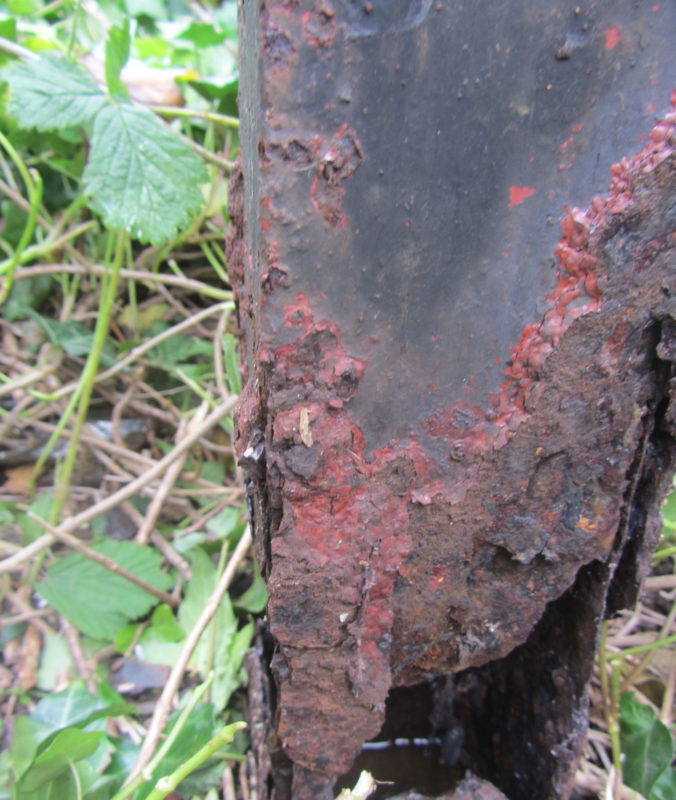
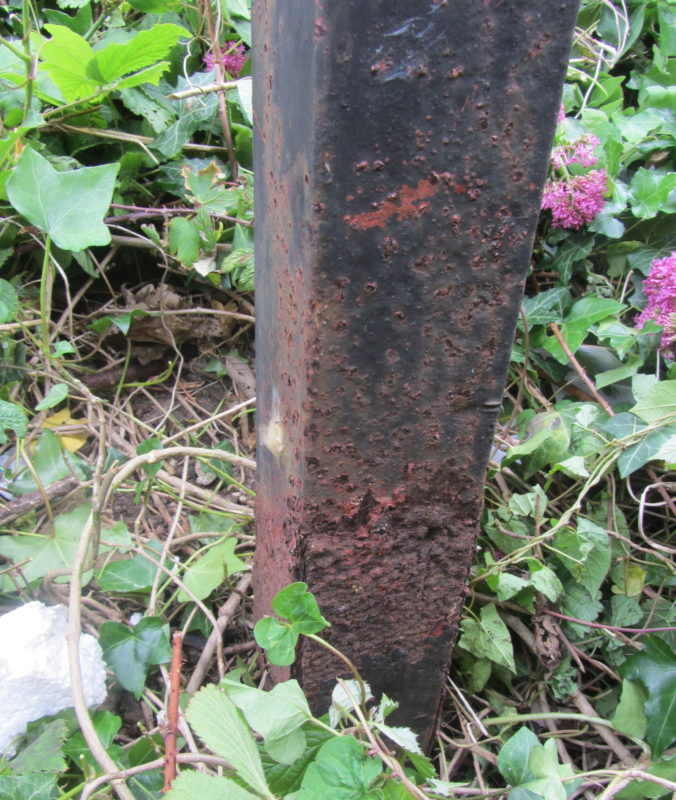
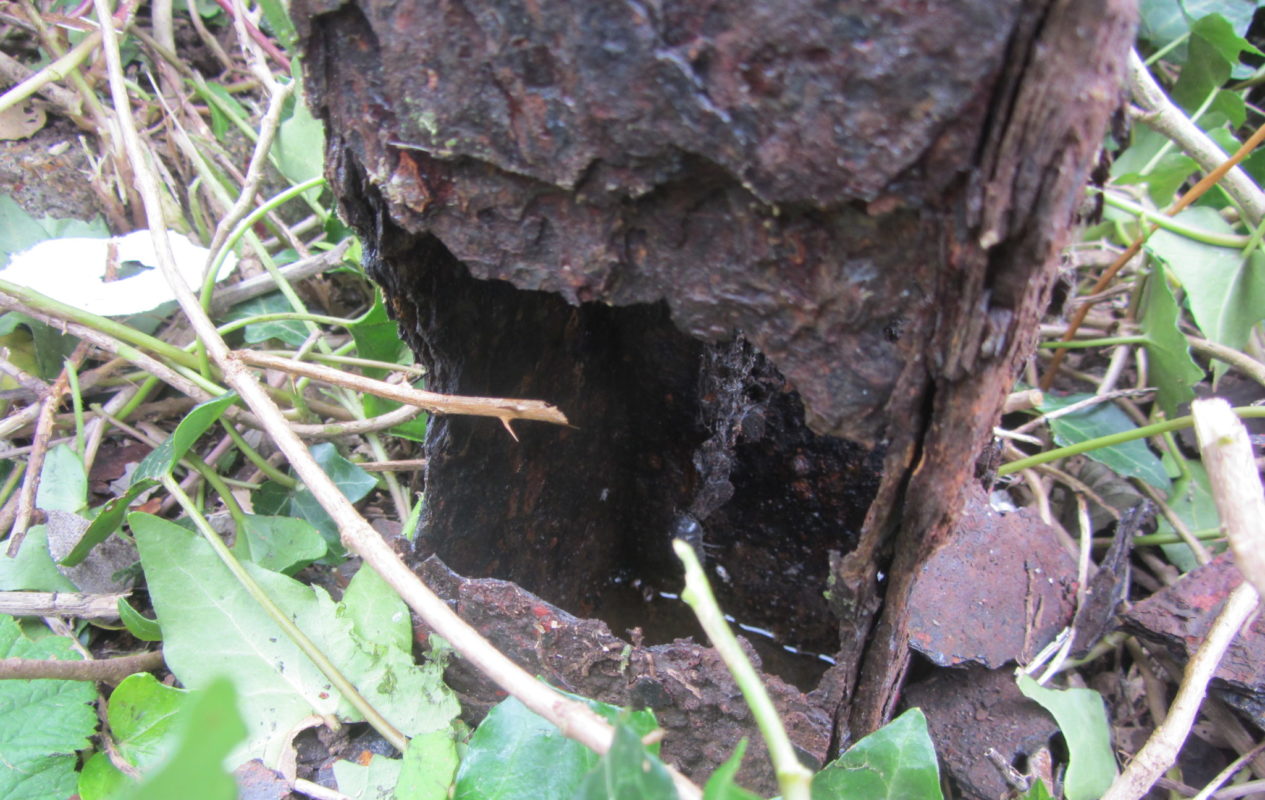
The Technical Solution
The staircase needed extensive remedial works which effectively involved taking it all apart and sanding back the corrosion to clean metal and putting it back to together with new fixings, whilst applying a new primer and topcoat system.
The corroded columns were to be cut back to an appropriate height and replaced with concrete plinth type foundations.
The benefit of this solution is that concrete is very durable and we can get the steelwork well above ground level where prone to corrosion.
This was fairly intensive work and would estimate around £5k, whereas a replacement staircase would be around £15-20k.
I would anticipate around 10-20 years additional life to this structure, providing that is well maintained.
How We Helped The Client
The main way we helped the client is by allowing them to keep the current staircase in use whilst they sought remedial quotes. Normally we use a traffic light system to advise the client on the structural status.
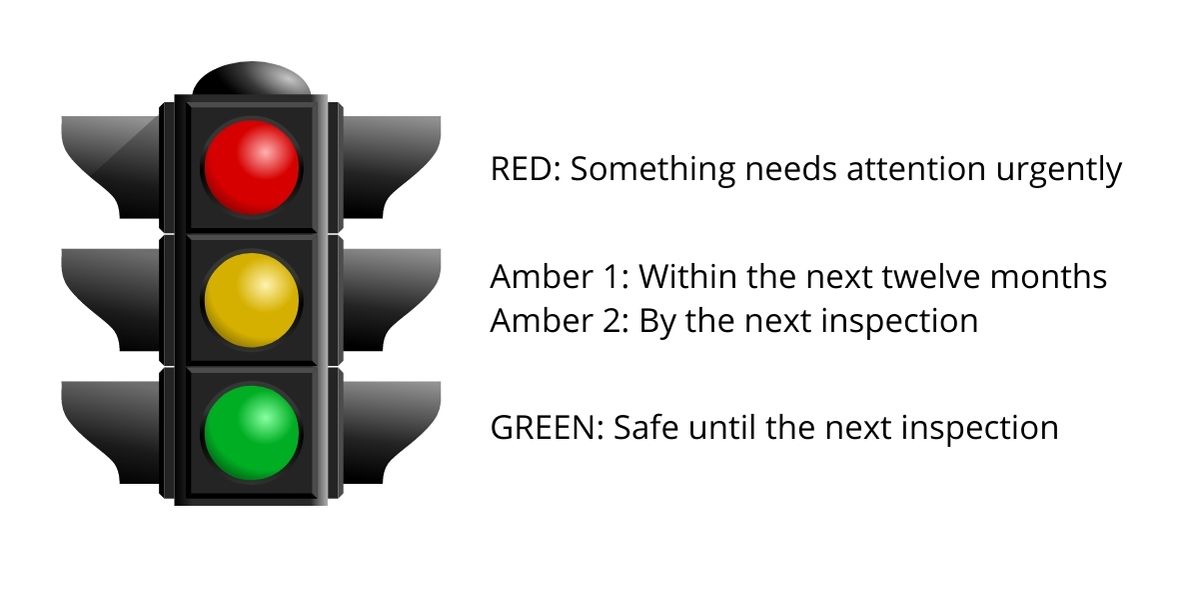
Ordinarily two failed columns would usually be assigned a RED – i.e the structure is condemned.
Structural Expertise
However, our structural design capabilities set us apart from other surveyors carrying out this role and we were able to assess the remaining two columns.
We found these to be adequate in supporting the structure in the short term which meant we could categorise the staircase as;
AMBER 1 – which meant the staircase needed urgent work within the next 12 months – but it could be kept in use for the short term, whilst works were organised.
The main benefit to the client was that they did not need to update their fire plan and reorganised escape routes. Which could ultimately lead to additional protection to create new routes, suppression or even closing off an area until repairs are carried out.
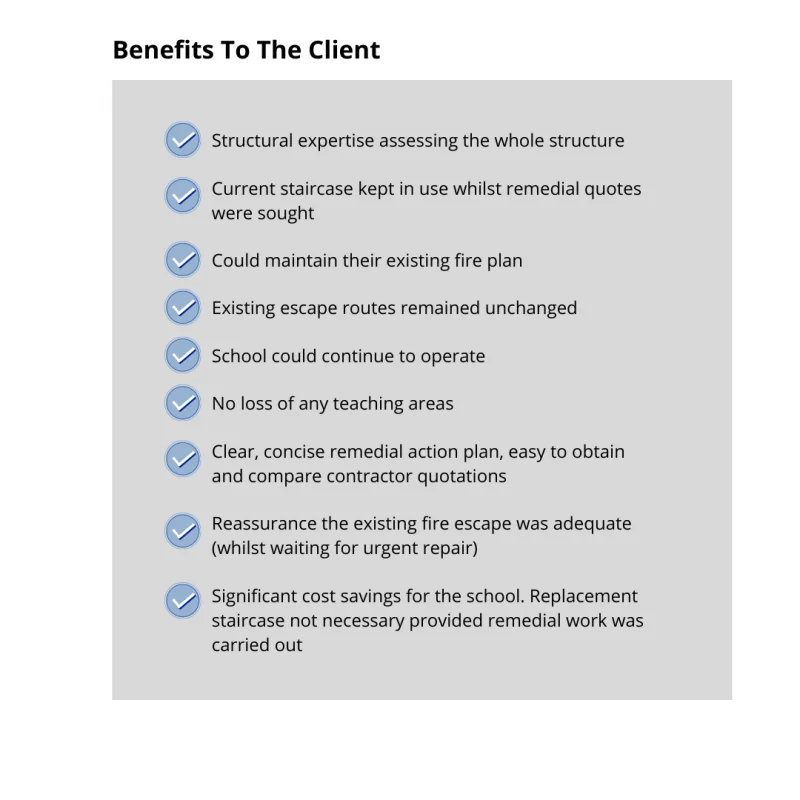
External Fire Escape Inspections
Are you a building owner?
Do you mange the health and safety of people in and about your building(s)?So that we can understand your requirements, it’s easier to talk.
Either call us on 0118 962 9666 or simply fill in your details below and we’ll get back to you at your convenience.
Please note, for one off inspections we generally work within a 50 mile radius of Reading. For multiple sites we work nationwide.
Click here to check out other Blog Post regarding external fire escape inspections.
Contact us